Premier Co-op
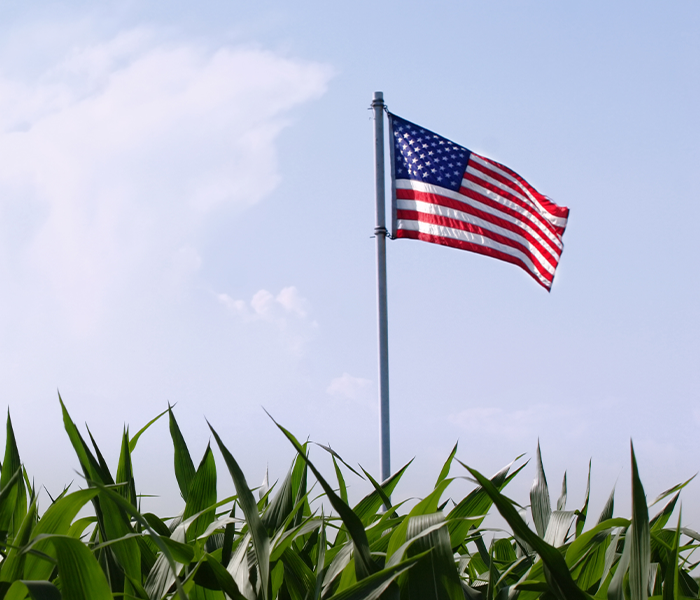
From the Manager's Desk
I hope everyone had the chance to enjoy the Independence Day holiday with family and friends. Thanks to all of you who called in your orders early and helped minimize the added pressure...
At Premier Cooperative, we have always viewed safety and compliance as a priority, both from an employee work environment standpoint, as well as ensuring that the products we bring to your farm are free of contamination and of the mix consistency and quality that you have come to expect. With ever increasing expectations and new regulations from the Food Safety Modernization Act, the VFD Law, and FDA inspections, about 5 years ago Premier Cooperative took the next step to make sure that we are doing all we can in regards to safety and compliance.
The Premier Cooperative feed manufacturing locations in Mineral Point and Westby are part of a small and elite group of feed locations that have received a HACCP (Hazard Analysis Critical Control Point) certification. HACCP is a management system in which food and feed safety is addressed through the analysis and control of biological, chemical, and physical hazards from raw material production, procurement and handling, to manufacturing, distribution and consumption of the finished product.
Obtaining the certification was not a small undertaking and the system continues to be evaluated annually. Each year the HACCP committee reviews any issues from the previous year and makes recommendations on any changes or additions to current practices that need to be made as facilities make changes or expand. Many records are kept and reviewed to ensure that the proposed practices are being completed. Monthly training is done at both the Mineral Point and Westby locations to train employees so all know what is expected of them.
Annually the team looks at all areas of the feed mill and conducts a risk assessment. The assessment addresses potential risks throughout the flow of products through the mill. Starting with before we receive ingredients, then receiving the ingredients, to the ingredients going through the mill and manufacturing, and finishing up with storage and delivery. It also addressed our employee training, our quality control and testing procedures, the record keeping system to verify traceability and to be able to recall product if that was ever needed. The assessment also looks at cleaning procedures, facility security, biosecurity, pest management and many other areas. Biosecurity continues to be an area of top priority at Premier and some changes have been made over the past few years to help give our customers confidence that the feed we deliver will be free of any physical contamination and help reduce the potential for disease transmission.
After the team finishes its work, there is a 3rd party audit and we have continued to pass our certification with very high marks. All of this is done to give you the confidence in knowing that Premier is committed to the safety of our employees and committed to delivering the highest quality products to your farm. The Mineral Point and Westby locations will continue to work on their HAACP certifications, knowing that minimizing animal stress by delivering consistent feed is one piece of the puzzle that can help you be more profitable.